Breakthrough Flow
We will explain the patented flow that further improves the performance of CO2 separation, concentration, and capture using the Wet-TSA method.
In the case of the rotor rotating type, the rotor is divided into an adsorption zone, capture zone, and desorption zone in the direction of rotation as shown in the figure, and the zones are sealed while the rotor rotates.
1. Air is passed through the adsorption zone to adsorb CO2.
2. When saturated steam at about 100°C is introduced into the desorption zone, the condensation heat of the saturated steam desorbs the CO2 adsorbed on the rotor.
3. The desorbed CO2 is passed through the capture zone and captured.
The secret benefit of this patented flow
By passing the mixed gas of desorbed CO2 and steam through the capture zone at the front of the rotation direction,
① As the rotor rotates, gas in the rotor gaps and adsorbed oxygen are expelled in the capture zone, preventing oxygen from entering the desorption zone, which is the hottest, and thermal oxidation deterioration is avoided.
② The mixed gas at the outlet of the desorption zone still contains sufficient saturated steam, so it has the effect of preheating and heat recovery before the desorption zone.
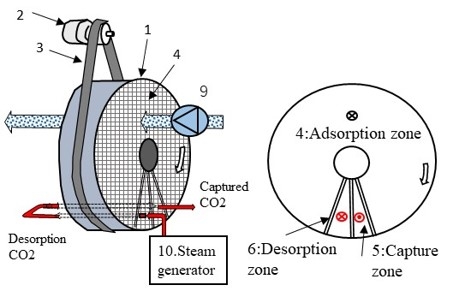